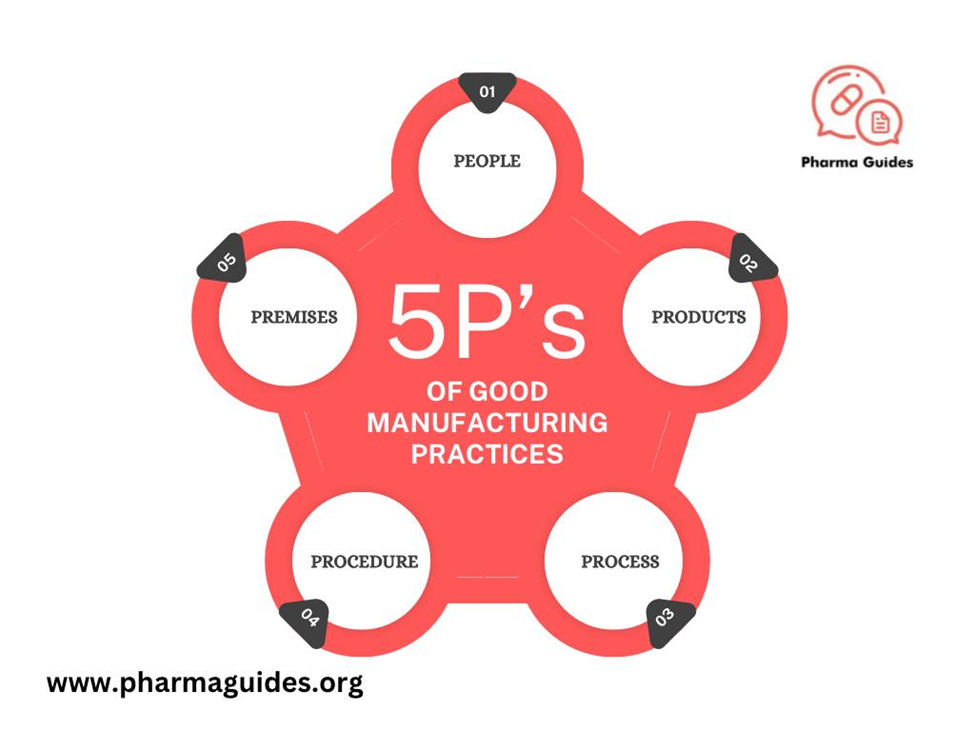
Below are the 5P’s of GMP;
People: The first P emphasizes the importance of personnel. It involves ensuring that staff are appropriately trained, qualified, and supervised for the tasks they perform. This includes training in GMP procedures, hygiene practices, and quality control measures.
Products: This P emphasizes the quality of the final products. GMP requires that products are consistently manufactured and controlled to meet quality standards. This involves using approved raw materials, following specified procedures, conducting in-process testing, and ensuring proper labeling and packaging.
Processes: The third P focuses on manufacturing processes. This includes having documented procedures for each step of production, ensuring consistency, accuracy, and reproducibility of manufacturing operations. Processes should be validated to demonstrate their effectiveness and reliability.
Procedures: The last P refers to documented procedures and records. GMP emphasizes the importance of maintaining detailed records of all aspects of production and quality control. This includes records of manufacturing processes, testing results, deviations, complaints, and corrective actions. Standard operating procedures (SOPs) are essential to ensure consistency and compliance.
Premises: This refers to the physical facilities where manufacturing takes place. Premises must be designed, maintained, and equipped to support the production of quality products. This includes considerations like cleanliness, adequate space, proper ventilation, and separation of different production areas to prevent contamination.
These 5 P’s collectively form the foundation of GMP and are crucial for ensuring the safety, quality, and efficacy of manufactured products across various industries. Adhering to these principles helps companies meet regulatory requirements and build trust with consumers by consistently delivering high-quality products.